Revolution Energy Services utilize in-house personnel for all our maintenance and repair services. We provide our customers with an end to end service and support solution for their job sites. These support services relieve our customers from the burden of utilizing their own personnel, stocking inventory, managing their assets, relieving supply chain issues, and hiring additional personnel for set up and tear down services.
- Fabrication Revolution Energy Services in-house fabrication services allow for greater customization of products and components to meet specific design requirements. It also provides flexibility to adapt quickly to changes in design or production needs.
- Direct company oversight of the fabrication process allows for better control over quality assurance. This results in higher-quality products, reduced defects, and improved customer satisfaction. We build zipper skids, cages, saddles, provide welding services and customized fabrication per our customer’s specifications.
- A customer’s supply chain issues can be minimized, and in-house fabrication can provide faster turnaround times for components or finished products. Our in-house fabrication team is better positioned to tackle unique or complex projects that may require a deep understanding of the company’s specific requirements.
- Asset Management Revolution Energy Services Asset Management services provide our customers peace of mind in knowing what products are being utilized on their jobsite while maintaining required documentation on a secure cloud server that is accessible 24/7 from anywhere. A product’s maintenance record is an asset that contributes to improved performance, reliability, cost management, and overall operational efficiency. It also plays a role in meeting regulatory requirements, ensuring safety, and enhancing the product’s lifecycle.
Documentation provided by this service:
- Each piece of equipment is digitized with QR Codes and serial numbers that are put on metal plates. This process ensures clear and durable identification for traceability.
- All repairs on equipment are kept in a file that is stored in the cloud.
- This process maintains comprehensive documentation for API specifications, including material certificates, test reports, and inspection records to ensure transparency.
At the click of a button company personnel can scan a QR code and know all equipment that is utilized on the pad. Our customers save time, personnel hours, and money by implementing effective Product Asset Management practices.
- Repairs Our internal in-house repair department is responsible for testing and repairing each piece of equipment after each job is completed. This non-destructive testing involves the processes of identifying, repairing, and validating the functionality of components within a machine or mechanical system to ensure no loss of integrity. This aspect of maintenance and reliability engineering ensures that machinery and all its parts operate efficiently and safely.
- Following our inspection and repair, documentation is prepared and stored in the cloud for easy access. Rely on the expertise of our Revolution Energy Services team of experienced repair and maintenance personnel and know your equipment is serviced and ready to go to the next jobsite.
- 3rd Party Labor The Revolution Energy Services roustabout and manual labor pool help our customers with a variety tasks such as inspecting equipment, cleaning work areas, and making repairs to ensure the safety and proper function of the machines and tools on the worksite.
- Because our personnel work in the industry, they are efficient at set up and tear down of a well pad. This understanding and repetitiveness of the process helps to minimize downtime for our customers.
Our maintenance and repair services take the burden of managing and maintaining equipment. Put our experienced team to work for you!
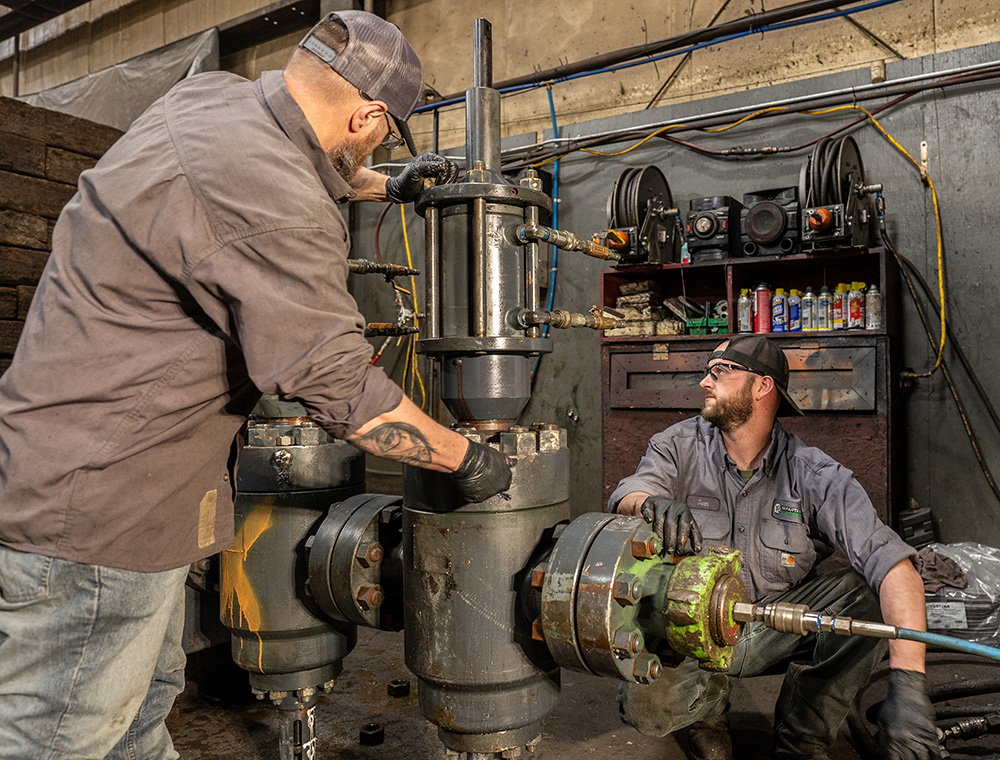
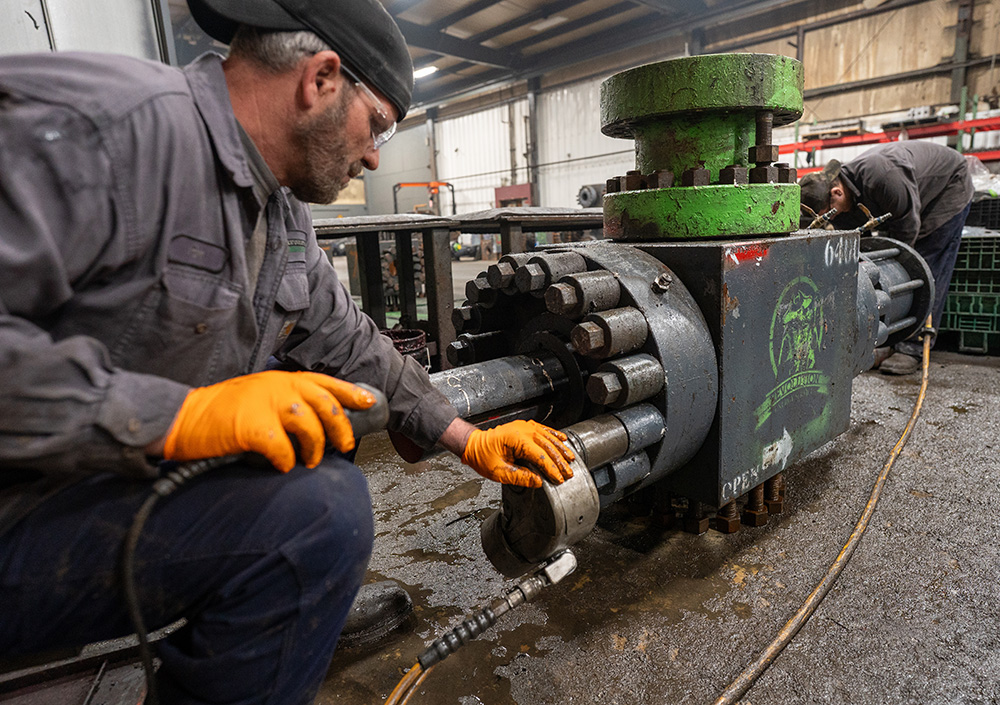