Frack Stacks
RES PROVIDES STATE OF THE ART API A1 MANUFACTURED PRESSURE CONTROL EQUIPMENT DESIGNED TO SERVICE PUMPING CONDITIONS RANGING FROM 5,000 PSI TO 15,000 PSI:
- Frac Stacks (5-1/8″ to 7-1/16″)
- Gate Valves (5-1/8″ to 7-1/16″) – Hydraulic and Ball-Screw Operated
- Goatheads (6-Port or 4-Port)
- Crosses – Tailored to Customers Operations
- Gate Valves (1-13/16″ to 4-1/16″)
- Spools – Multiple different sizes ranging from 16 inches to 10 feet
- Zipper Manifolds
- Flex Hoses – Lengths up to 20 Feet
- Accumulators
- Automated Greasing Manifolds
- Quality Control for valves and critical machine parts ensures that they meet the required standards, operate reliably, and contribute to the overall integrity of the system. In-house Revolution Energy Services personnel complete all maintenance on each piece of equipment. These are some checkpoints used by our in-house personnel:
- Material Quality: Valve materials are verified to meet industry standards and specifications. This ensures materials are resistant to corrosion, erosion, and other environmental factors.
- Manufacturing Processes: Adherence to casting, forging, and machining standards are verified and checked.
- Dimensional Accuracy: Critical dimensions such as bore diameter, face-to-face dimensions, and flange dimensions are checked.
- Pressure Testing: Valves are pressure tested to ensure they can withstand operating pressures without leakage.
- Leakage Prevention: Stringent leak testing procedures are implemented to verify the tightness of valve seals.
- Functional Testing: Valves are tested in various positions and under different flow conditions.
- Seal Integrity: Inspection and testing of seals, gaskets, and packing is performed to ensure they maintain integrity under operational conditions.
- Surface Finish: Valve surfaces are examined for defects or irregularities to ensure they have the required finish to prevent corrosion and improve wear resistance.
- Compliance with Standards: Valve testing must comply with relevant industry standards, such as API, ASME, and ISO. Our employees stay up to date on changes in standards and incorporate them into our quality control processes.
- Supplier Quality Assurance: A robust supplier quality assurance program is implemented to ensure that components supplied by external vendors meet our quality standards. In-house Revolution Energy Services personnel regularly audit and assess the performance of valve suppliers.
- Valve Performance in the oil and gas industry ensures safe, efficient, and reliable operations for our employees and our customers. Key integrity features include:
- Reliability: Valves must reliably control the flow of fluids, gases, or multiphase substances. This minimizes the risk of leaks or operational failures, contributing to the overall safety and integrity of the system.
- Durability and Longevity: Valves must withstand the harsh conditions of the oil and gas industry, including high pressures, temperatures, corrosive substances, and frequent operation. Durability ensures a longer service life, reduces maintenance requirements, and minimizes a customer’s downtime.
- Compatibility: Valves should be compatible with the specific characteristics of the transported fluids or gases. This includes considerations such as temperature, pressure, corrosiveness, and composition.
- Regulatory Compliance: Valves must meet industry standards and regulatory requirements to ensure the safety and environmental compliance of the entire system. Compliance with standards such as API (American Petroleum Institute) is often crucial.
- Ease of Maintenance: Efficient maintenance is essential for minimizing downtime and ensures continuous operations. Valves designed for easy inspection, repair, and replacement provide a quick turnaround during maintenance activities.
- Energy Efficiency: Valves play a role in the energy efficiency of a system. Properly designed and maintained valves contribute to efficient energy utilization, especially in processes where pressure and flow control impact overall energy consumption.
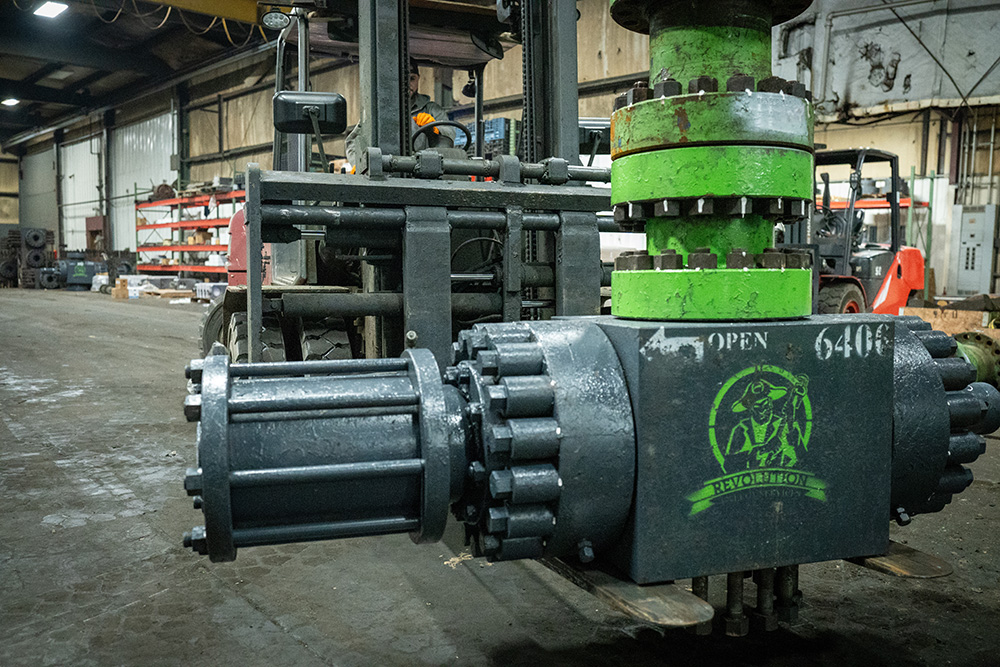
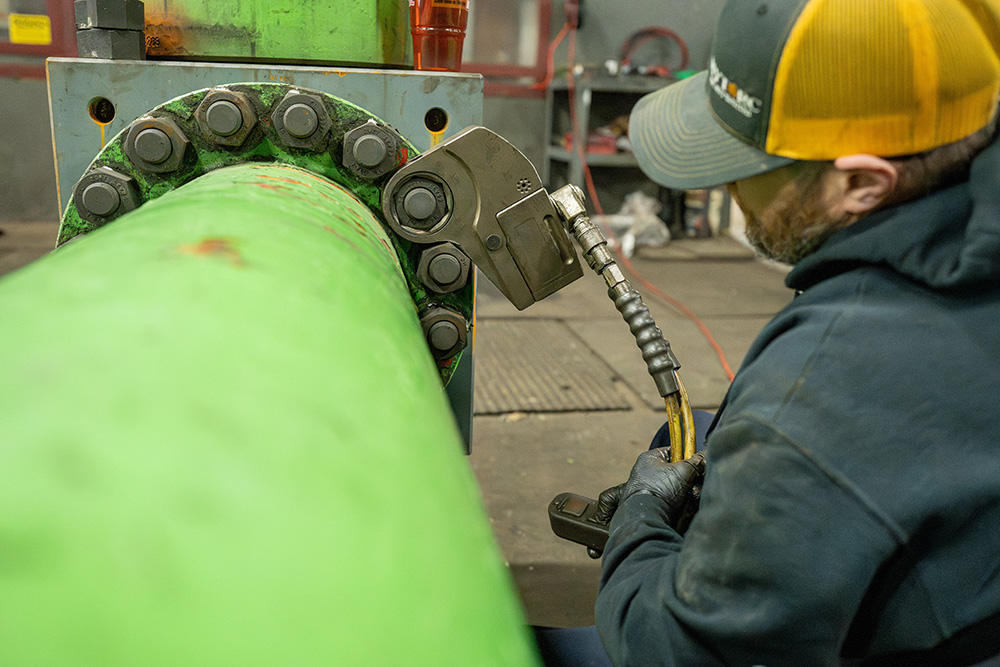
- Non-Productive Time Reduction (NPT) enhances operational efficiency and minimizes costs. Revolution Energy Services helps our customers minimize NPT and realize a higher level of operational efficiency that may result in higher profitability. Key components of this process include:
- Proactive Maintenance: Our in-house maintenance department implements predictive and preventive maintenance strategies to address equipment issues before they lead to unplanned downtime. We conduct regular inspections and replace or repair components proactively.
- Reliability-Centered Maintenance (RCM): We utilize RCM principles to prioritize maintenance tasks based on their impact on system reliability and performance.
- Training and Competency: Our personnel are provided ongoing training to enhance their skills in equipment operation, maintenance, and troubleshooting.
- Effective Communication: Our team is available when you need us most. We establish effective communication channels for reporting and addressing issues promptly. Feedback from employees is encouraged to gather insights into potential areas for improvement.
- Inventory Management: An optimal inventory of critical spare parts is maintained to minimize delays in equipment repairs. Equipment sourcing is done by Revolution Energy Services in-house personnel which minimizes the need for customers to carry product inventory. Our in-house fabrication team repairs parts to ensure timely availability of necessary components.
Revolutions Energy Services frac equipment support services is second to none in quality and performance while minimizing nonproductive time for our customers.